Hello and welcome to RepRap Ltd’s website and blog.
We will use this blog to document the research and development RepRap Ltd are working on.
We are planning to work on both RepRap development and also other areas, but using RepRaps for prototyping and testing.
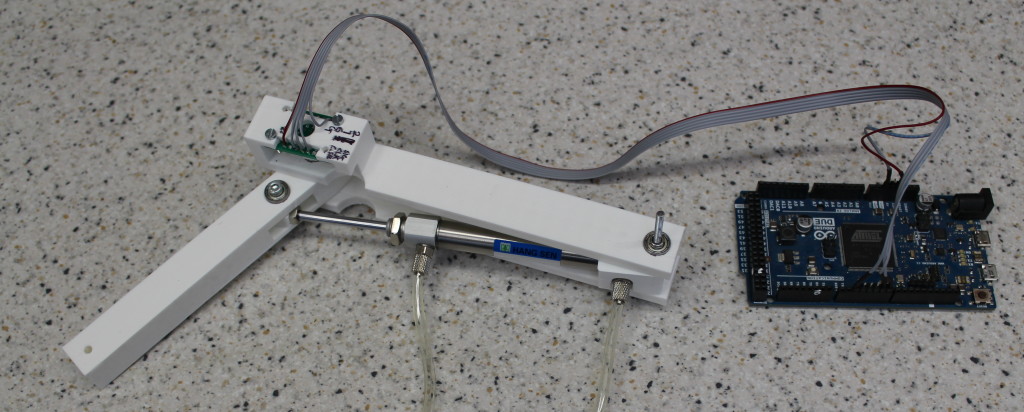
As an example of the sort of projects we are working on, here is a testbed pneumatic robot joint. Most low-cost robots rely on electric servos or steppers. But these have poor torque and speed, and no power amplification. Pneumatics, in contrast, offer the possibility of developing Boston Dynamics style robots. And with the power of modern microcontrollers these could also be low-cost if only pneumatic servos and valves were low-cost.
The joint above has a conventional actuator and valve (not shown), and is intended just to set up the control system, which relies on the magnetic rotary encoders from AMS. When we have got this working we will be replacing the actuator and valve with 3D-printed equivalents to see if we can match the performance of their conventional counterparts.
Gas-tight FFF 3D prints are tricky to make, as is well-known. But we think that, with the addition of just a few non-printed parts like O rings, short lengths of plastic plumbing pipe, and silicone tube, we can make a very modular parametric pneumatic control system.
Connect with us
Keep up to date on the latest RepRap Ltd news:
Very interesting post 🙂 I care about another thing: Can we successfully use pneumatic actuators to control the axes of a 3D printer? Has anyone tried similar things ? 🙂
It might be possible to make a pneumatic 3D printer (though it would be difficult). But a 3D printer doesn’t need the principal advantage that pneumatics has over electrical drives, which is power amplification. A 3D printer runs continuously at a pretty constant level of power consumption. But (say) a walking robot may have a low average power consumption, but need short sharp bursts of very high power. It is for this sort of thing that pneumatics wins over electrical drives. This is even true if the air compressor is electric.
Linear actuators are basic budinilg blocks as manufacturing automation equipment. The linear actuator directs a force that it receives from another device into a straight line in order to perform a task. If the actuator is powered by electricity, it will turn that force into a straight line force. That is very straightforward. If the actuator is powered by hydraulics, it will do the same thing with the power, convert it into a straight line. There are different of sources of power for the linear actuator that is used as manufacturing automation equipment. Driving power from pneumatics, electricity, or hydraulics are the sources. The selection of any one of these sources is usually dictated by the type of application in which it will be employed, the budget for the application, and the performance required.for more details
Very interesting idea. If the pneumatic drives can be made low cost and reliable, then this would usher in a new revolution just like you did with open source 3D printing.
All the best from our small team at Alfatek!
Interesting and could really make pneumatics and low pressure hydraulics more widely available to the consumer, I look forward to future updates on the project.