How can we correct for every single inaccuracy, non-linearity, bend in an axis slider, error in steps-per-millimeter and all the rest in a RepRap machine using just one technique? Read on… Here’s me, deliberately blocking the nozzle of my RepRap Fisher.
Making RepRaps More Accurate
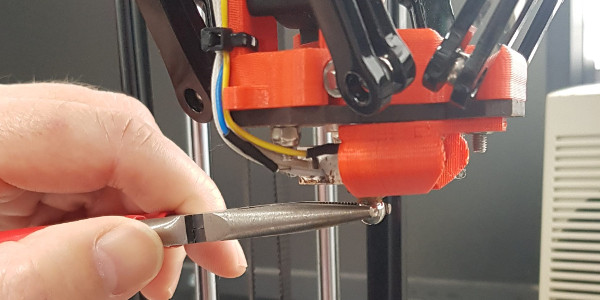