Goal
By the end of this section, your Huxley Duo should be mechanically and electrically complete, and ready for commissioning. |
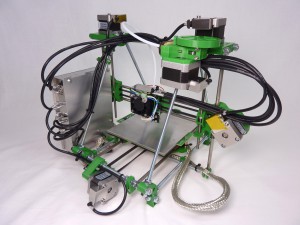 |
Wiring the printer
CAUTION: Never plug in or unplug motors or heaters when the power is on or the USB is plugged in.
Especially with the motors, you risk damaging the motor driver chip, and rendering the whole Duet board useless. This includes unplugging the motor end of the loom, too. A good rule is ALWAYS to turn off the power and to unplug the USB when connecting or disconnecting ANYTHING from the board.
Wiring diagram
The instructions below show the fitting of the wiring. If in doubt, refer to this wiring diagram.

Fitting the wiring looms
RepRapPro Huxley Duo printer kits are supplied with pre-assembled wiring looms. It’s easiest to fit these at the terminating end, route them back to the Duet, before plugging them in, and finally tidying up the wiring. Labelling the wires will also help!
Heated bed wiring
# |
Component |
Qty |
Type |
785 |
Heated bed wiring loom |
1 |
Wiring |
|
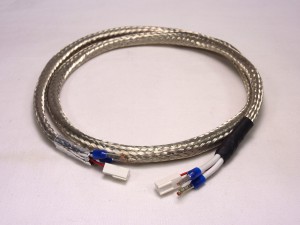 |
Start by connecting the heated bed loom at the Duet end. Use the end of the loom with the silver tape on it; this goes in the notch in the enclosure perimeter, and provides the earth for the loom braiding. The white wires can go into the screw terminal either way around; polarity is not important on the heated bed. The thin red wires are for the bed thermistor. |
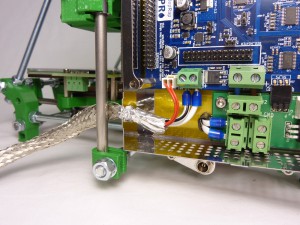 |
Run the loom across the bottom of the printer. Attach with cable ties at points where they will not hit the belt or Y carriage. |
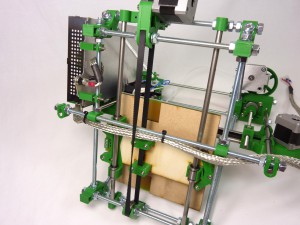 |
Remove the heated bed by unscrewing the three M3 cap head screws, which mount it on the Y carriage. |
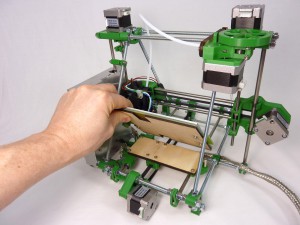 |
Removing it from the frame is easiest done as shown. |
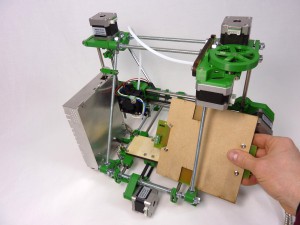 |
Connect the heated bed wiring loom to the heated bed. The wiring loom uses the outer two (of three) screw terminals. The thermistor wires connect to the two pins furthest from the edge of the board. Note the orientation of the thermistor wire housing; if you put it on the other way around, it fouls on the hex stand-off when you try to reattach the bed. |
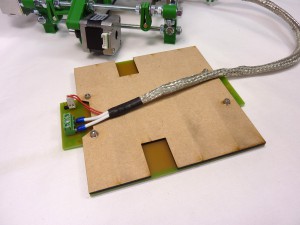 |
Replace the bed, routing the heated bed loom as shown. Attach the bed loom to the Y carriage, and to the frame, as shown, with cable ties. |
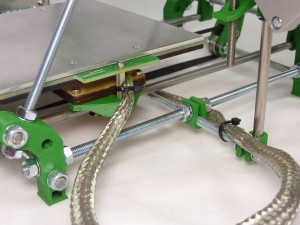 |
It is very important that the bed loom is free to move, and does not catch on anything. It also needs to bend, but without hinging in one place – if it does, the wires will fatigue over time, and eventually break. |
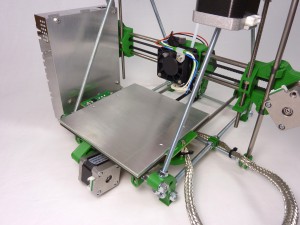 |
Slide the Y carriage back and forth, making sure the bed loom moves smoothly along the full range of the Y axis. |
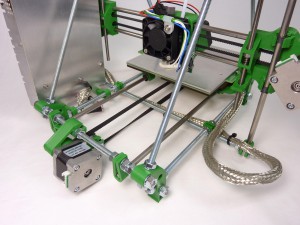 |
Y-endstop loom
# |
Component |
Qty |
Type |
791 |
Y-endstop-loom |
1 |
Wiring |
185 |
Microswitch |
1 |
Electronics |
918 |
#4 round head screw |
2 |
Fastener |
212 |
M3 washer |
as required |
Fastener |
|
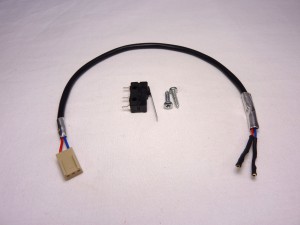 |
We have to make a couple of modifications to the microswitch, in order for it to fit. First, cut 5mm from the end of the lever. |
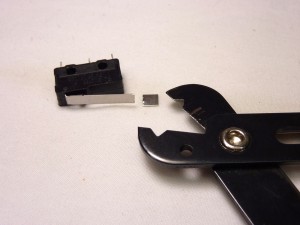 |
This is so that it fits correctly. Otherwise, the lever fouls on the Y smooth rod. |
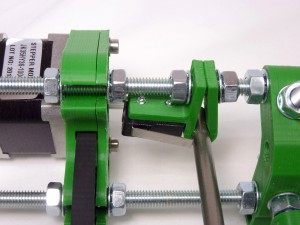 |
Next, drill the mounting holes out with a 3mm drill. This allows the supplied #4 screws to fit through easily. |
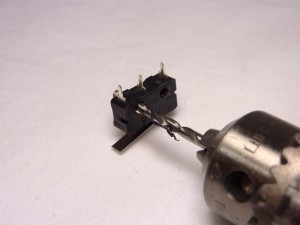 |
Fit the microswitch to the tabbed Y-rod-clamp, using the #4 round head screws. The screws need a few washers under their heads to stop the ends touching the cross bar and/or nut; without them the y-rod-clamp will push over out of alignment. We will be updating the printed part soon, for better fit. |
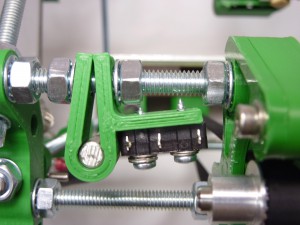 |
Check the Y-carriage makes contact with the endstop. Move it to the end, and as it touches the endstop, the microswitch should make a small ‘click’. Make sure the microswirch lever is not too long, and gets stuck on the Y smooth rod; if so, cut it a little shorter. |
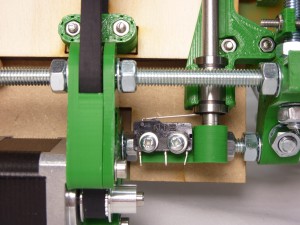 |
Connect the Y endstop wiring to the OUTER two pins of the microswitch. If they are a little loose, and won’t stay on, use a pair of pliers to lightly crush the crimp on the loom, to make the fit tighter.We only use a microswitch endstop for the y-axis; the x- and z- axis use the proximity sensor to sense where the end of the axis is (the ‘home’ position). |
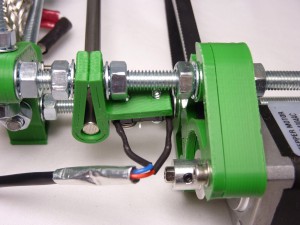 |
Motor wiring looms
# |
Component |
Qty |
Type |
587 |
x-motor-loom (685mm) |
1 |
Wiring |
589 |
y-motor-loom (395mm) |
1 |
Wiring |
589 |
z1-motor-loom (395mm) |
1 |
Wiring |
789 |
z2-motor-loom (485mm) |
1 |
Wiring |
793 |
z3-motor-loom |
1 |
Wiring |
588 |
extruder-motor-loom (575mm) |
1 |
Wiring |
579 |
motor-shield |
5 |
Laser cut |
520 |
M3x35mm cap head screw |
5 |
Fastener |
|
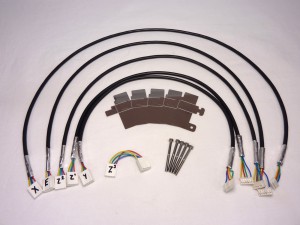 |
Take the six motor looms. Check the wiring order of the wires in the housings; if they have been assembled incorrectly, the motor will not run correctly. It’s a really good idea to mark the motor looms, this will make it easier to connect them to the Duet. From longest to shortest, they are X, Extruder, Z2, Z1, Y and Z3. Z1 and Y are the same length. |
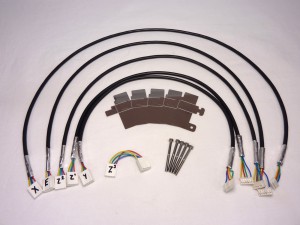 |
Take the five motor shields. Bend the first one, at 90 degrees along the score lines, as shown. You need four left-handed ones, and one right-handed one. Compare the one you have bent to the picture, and bend the other four appropriately. Try not to unbend them; they will fatigue and break after a couple of attempts. |
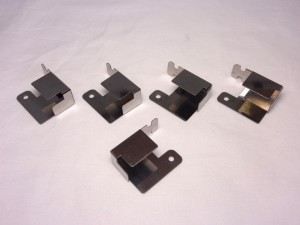 |
For each of the motors, you will need to remove one of the screws, to attach the shielding. Start with the Y motor, and remove the screw shown with a cross head screwdriver. |
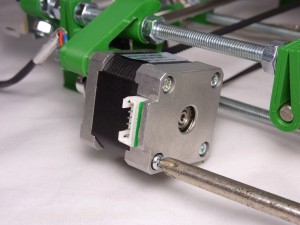 |
Take the Y motor loom (the shortest except for the very short z3-motor-loom), and connect it to the motor. Put a bend in the wire as shown. |
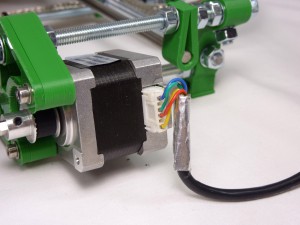 |
Take the motor shield (the one ‘right-handed’ shield), and place it over the connector. Secure with an M3x35mm cap head screw. |
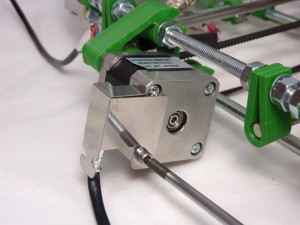 |
Finally, take a cable tie and put it around the loom, so the silver tape covering the end of the loom is trapped in the cable tie, and makes good contact with the shielding. This ensures the motor shielding is continuous, and very little electrical noise should escape. |
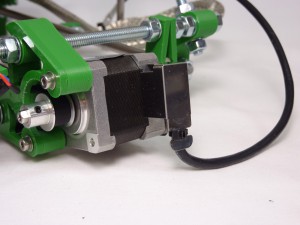 |
Route the y-motor-loom through the y-motor-mount. |
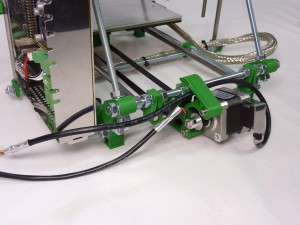 |
Connect the looms to the other motors in a similar fashion. The Z motor closest to the Duet uses z1-motor-loom, while the one next to the extruder uses the z2-motor-loom. |
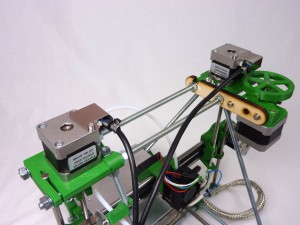 |
The extruder motor uses the next longest motor loom, and the X motor the longest. NOTE: your X motor probably has the connector facing a different direction. It will need to be rotated 180 degrees, so the connector is on the side shown. Simply unscrew the two motor mounting screws, rotate the motor, and do them back up again. |
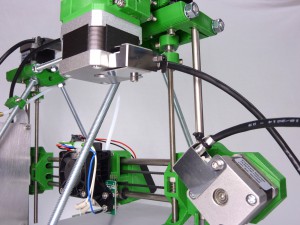 |
The extruder-motor-loom and x-motor-loom go through the gap between the extruder motor and the frame. |
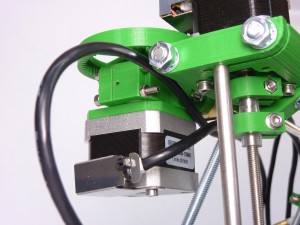 |
Leave enough slack in the x-motor-loom for the X axis to move up and down in Z. |
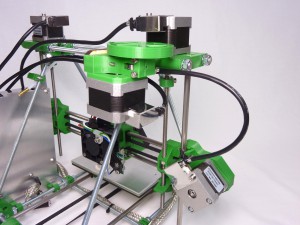 |
Loosely hold the Z, X and extruder looms in place with a cable tie. |
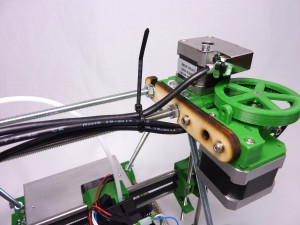 |
Proximity sensor and loom
# |
Component |
Qty |
Type |
790 |
Proximity sensor wiring loom |
1 |
Wiring |
545 |
Proximity sensor |
1 |
Electronics |
242 |
M3x16mm cap head screw |
2 |
Fastener |
258 |
M3 nut |
4 |
Fastener |
|
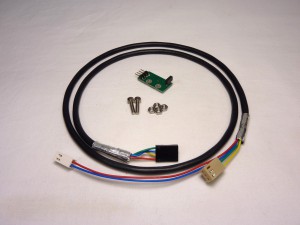 |
The proximity sensor is a small PCB, with four pins on the end of the board. Make sure the sensor itself, the black part at the other end from the pins, is standing perpendicular to the board; they can get bent over in transit. Push the two M3x16mm cap head screws through the board, and put an M3 nut on each, on the back. |
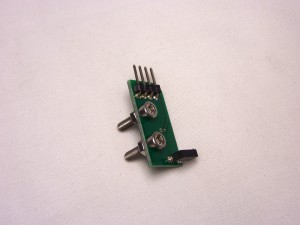 |
Attach the proximity sensor to the X carriage to the right of the hot end, through the two holes in the acrylic. Hold it in place with the other two M3 nuts. The first M3 nuts space the PCB away from the acrylic. The sensor should be on the side facing the X smooth rods. |
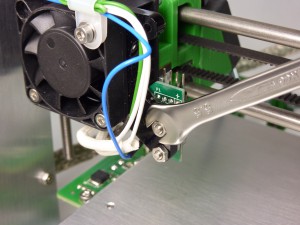 |
Connect the proximity sensor loom. NOTE: the sensor has a polarity; the order of the wires is VERY important. It should be as the picture, from left to right: green, blue, yellow, red. Red should be closest to the heatsink. The acrylic heatsink spacer has two holes in it, for a cable tie to hold the loom. Secure the loom as shown, making sure the loom is fully engaged on the sensor pins. |
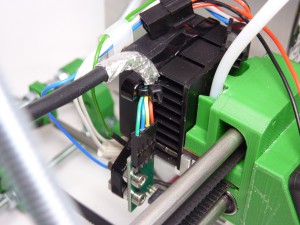 |
Hot end and fan looms
# |
Component |
Qty |
Type |
788 |
Hot end loom |
1 |
Wiring |
787 |
Fan loom |
1 |
Wiring |
891 |
Hot end enclosure |
1 |
Laser cut |
242 |
M3x16mm cap head screw |
1 |
Fastener |
|
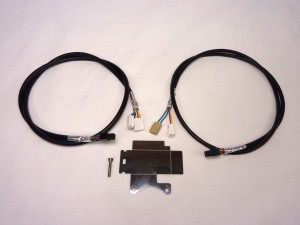 |
Connect the hot end and fan looms. The six-wire loom connects to the hot end plug, the four wire loom connects to the fans. |
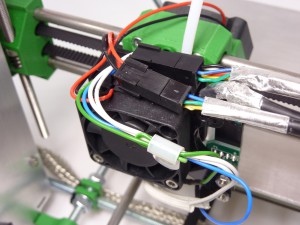 |
Bend the hot end enclosure as shown. Leave the end open – you will need to tuck some wires into it. |
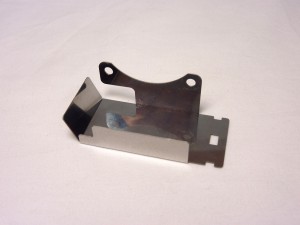 |
Fitting the enclosure, and getting the wires and housings to fit in neatly, can be quite fiddly. Assemble loosely, getting the wires in the right place, before screwing the enclosure into place with an M3x16mm cap head screw in the free fan hole, also using the existing M3x16mm cap head screw (which has the P-clip on it too). Fold the end of the shield so that it is at 90 degrees, and holds the wires in place. |
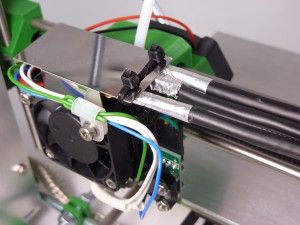 |
Cable tie the three looms to the shield. The metal tape on the end of the looms should be trapped in the cable ties. These provide strain relief for the wires. |
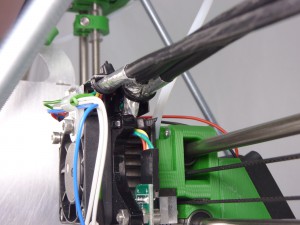 |
The hot end looms run between the X axis motor connector and the Z smooth rod. This gives them a straight path to follow, as the X axis moves back and forth. |
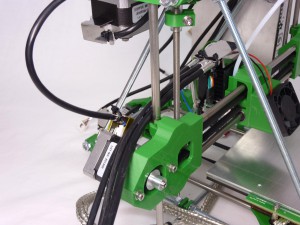 |
Feed the hot end cables through the triangular hole between the extruder motor and the frame. |
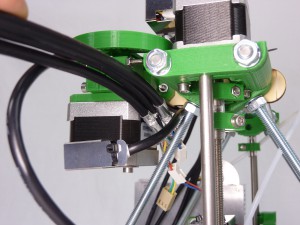 |
Cable tie the hot end looms, and the motor wires, lightly to the frame. Leave a generous loop (you will adjust this in the next steps) to allow the X carriage to move back and forth, and up and down. |
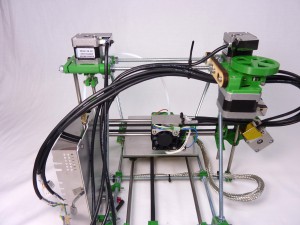 |
Connecting the looms to the Duet
For each axis, the Duet has 7 pins; 4 for the motor, three for the endstop (when needed). Check with the wiring diagram at the top of the page the orientation of the motor wire, and the exact pins it plugs into.
The Z axis plugs in on the lowest pins on the Duet. On Huxley Duo, the z-axis is a special case; it has two motors. The 5V regulator board has special pins. Connect the z3-motor-loom (the shortest) as shown. |
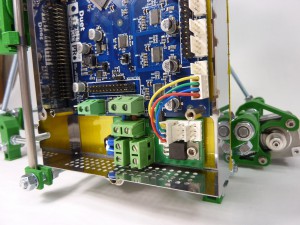 |
Connect z2-motor-loom to the the plug closest to the enclosure-perimeter. |
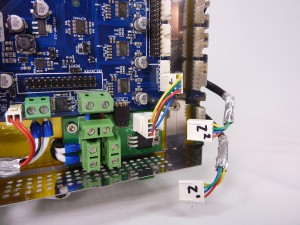 |
z1-motor-loom plugs in in the middle. |
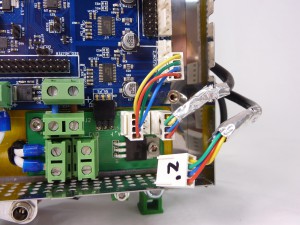 |
This shows the Z motor looms plugged in. |
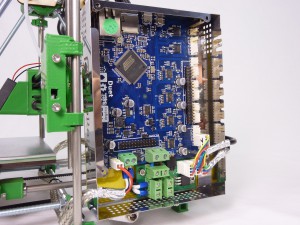 |
We’ll be plugging in the rest of the motors, in order, from bottom to top. Next is the Y axis motor loom. |
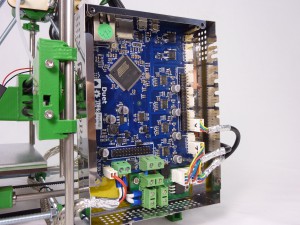 |
Then the X axis motor loom. |
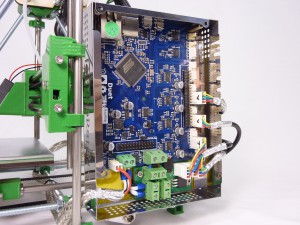 |
Then the extruder motor loom. |
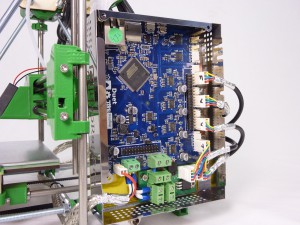 |
The Y endstop loom plugs in ABOVE the Y motor loom, BELOW the X motor loom. The Y endstop will not function if it is plugged in in the wrong place! |
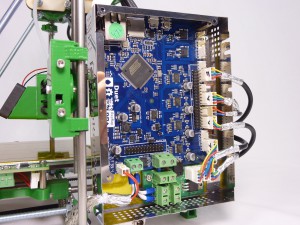 |
The proximity sensor loom has two connectors. The short wires plug in to a free endstop connection. You can use either the X endstop pins (above the X motor connection), or the extruder endstop pins (above the extruder motor connection), depending on where the gap in metal perimeter is. There have been a couple of different versions of the perimeter; the current version uses the extruder endstop pins, older versions use the X endstop pins (as shown in the picture).
The longer wires reach across the board, and plug into two pins in the expansion header. Check the wiring diagram at the top of the page to see exactly which pins. |
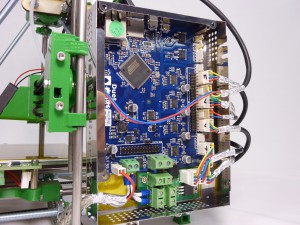 |
The hot end loom also has two connectors, one with four wires and on with two. It is VERY important that these are connected correctly, or you may damage the Duet. They connect ABOVE the Extruder motor loom, but not right next to it; leave the three pins immediately above the extruder motor loom free. Again, check with the wiring diagram above to get the correct pins. |
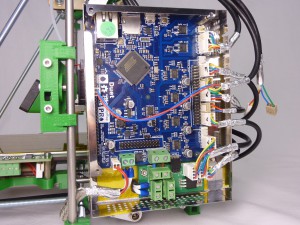 |
Pay particular attention when connecting the hot end heater and hot end thermistor connectors. If you put them in the wrong place, 19V (from the heater or fans) can run down the 3.3V line of the thermistor, and will immediately destroy the main processor chip. We regard this mistake as a user error, and is NOT covered by the warranty. Check your wiring! |
The hot end fan loom also has two connectors. Again, check with the wiring diagram above to get the correct pins. |
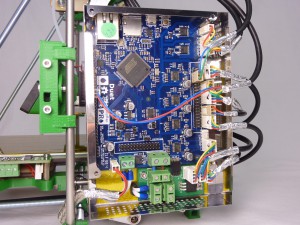 |
The cover in place. All the wires should sit in the slots in the enclosure perimeter, and the cover keeps them in contact for good grounding, as well as supporting the wires. You may want to leave the cover off (again), until after the commissioning stage (the next page of the instructions), as it is useful to be able to access the Duet board, ie to press ‘reset’, or check your wiring, during commissioning. |
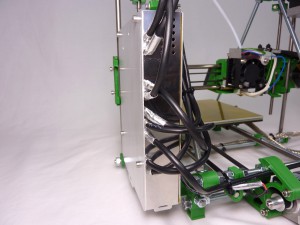 |
IMPORTANT: 5V JUMPER!
Fit the 2-way PCB jumper (a small, black, jumper block) on the two pins in the centre of the board, labelled ‘J10’ and ‘ATX_5V_EN’. Without this, the Duet board will not be supplied with power without the USB connected! |
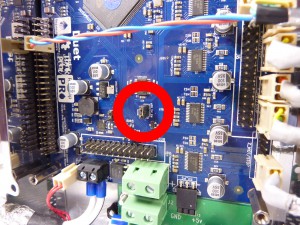 |
Wire routing
Use a couple of cable ties to hold the motor wires to the edge of the frame. |
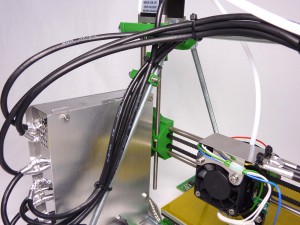 |
Use a couple more to hold all the wires at the top of the frame. |
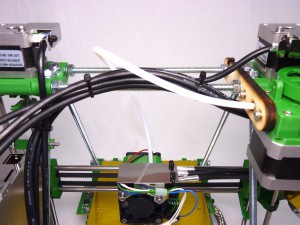 |
The looms going to the hot end (proximity sensor, hot end, hot end fans) need to slide through the gap between the X motor loom and the Z smooth rod, on top of the motor. Check they can do this freely. There needs to be enough slack in them, and the X motor loom, to cope with changes in the height of the X axis, too. Adjust as necessary. |
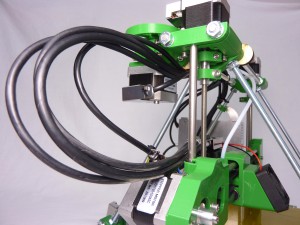 |
Test the movement of the x-axis along the full range of motion. Check the wires do not kink, or get caught. We’ve also put a piece of Kapton tape over the X motor shield, in case the sharp edges wear the wiring loom. |
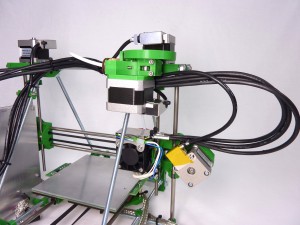 |
At the far end, check the wires don’t get caught. |
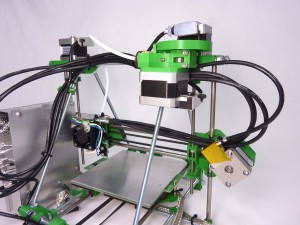 |
Attach the Y endstop and Y motor looms in place with a couple of cable ties. Make sure the bed can pass by them, without hitting them. |
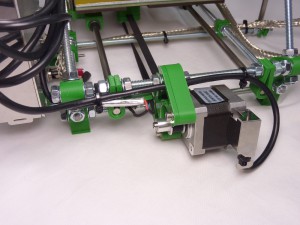 |
The finished wiring. |
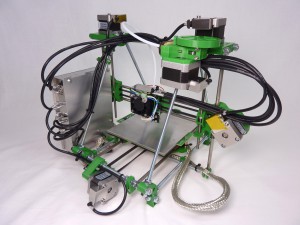 |
Preparing the print surface
Use the supplied Kapton tape. Attach it on one side the bed. Line it up with the edge of the bed. |
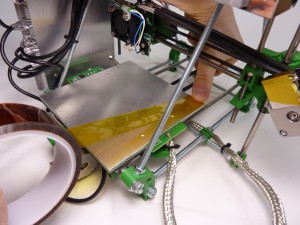 |
Gently lower the other end onto the bed, keeping a little tension in it. Smooth out any air bubbles. |
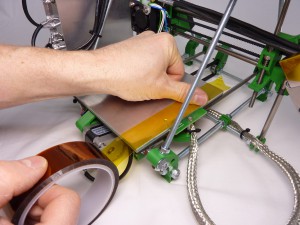 |
Cut the end with a sharp knife, along the edge of the bed. |
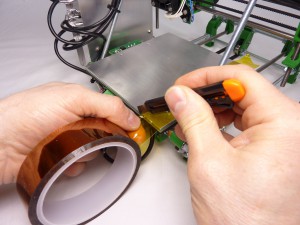 |
One strip down, five to go! |
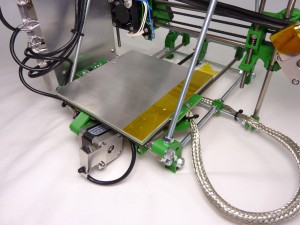 |
Start the next strip in the same way, as close as possible to the first strip, with as small a gap as possible between the strips. |
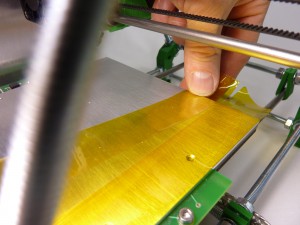 |
Continue across the bed. Try to make it as neat as possible. |
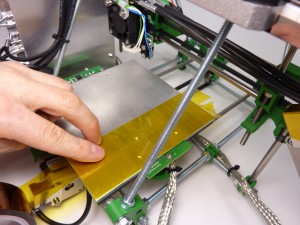 |
Trim the excess from around the edges. |
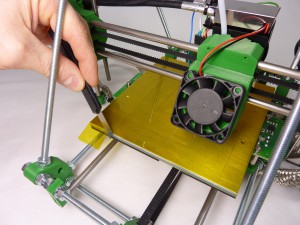 |
The bed surface needs to be completely free of all oil and grease (including finger marks), otherwise your prints won’t stick to it. Clean the surface with nail polish remover (containing acetone, glycerine, and as few other ingredients as possible, and definitely not lanolin or any other oil or grease) using a lint-free cloth. Other products that also work include pure acetone, isopropyl alcohol, white methylated spirits, white vinegar. All of these dissolve oil and grease before evaporating. Don’t use Windex/Windowlene or polish; they often have a non-stick component! |
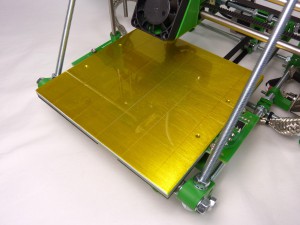 |
Check the Y carriage can move back and forth unhindered. |
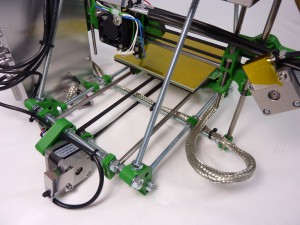 |
It’s also worth checking you haven’t knocked any wires loose. The thermistor wires, connecting the hot end thermistor to the wiring loom, are quite exposed. Check they are still connected correctly. |
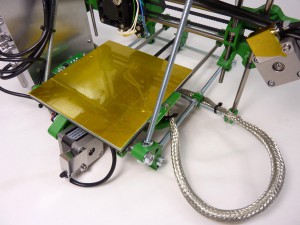 |
Wiring finished
The printer, showing the wiring complete. |
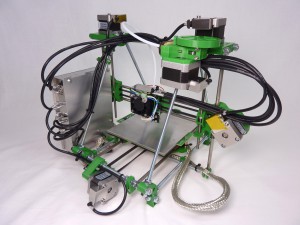 |