Goal
By the end of this stage, your machine will look like this: |
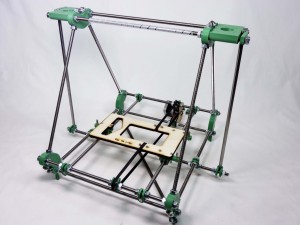 |
Y-carriage
# |
Component |
Qty |
Type |
914 |
Y bearing holder |
3 |
Printed |
923 |
Y belt clamp |
2 |
Laser cut |
915 |
Y sled |
1 |
Laser cut |
287 |
LM8UU Linear bearing |
3 |
Hardware |
818 |
M3x18mm Male/Female Stand Off |
3 |
Electronics |
241 |
M3x20mm cap head screw |
10 |
Fastener |
204 |
M3 Nyloc nut |
13 |
Fastener |
|
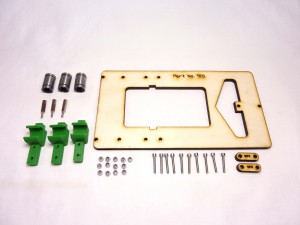 |
Y-carriage assembly
Insert two of the M3x20mm cap screws through the holes of the Y Sled as shown. |
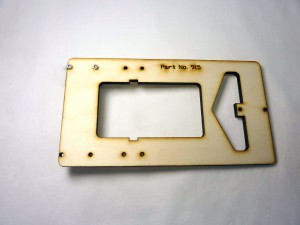 |
On the opposite side of the sled, insert the cap screws through the bearing holder, with the longer lug facing outwards as shown. Secure with 2X M3 nyloc nuts |
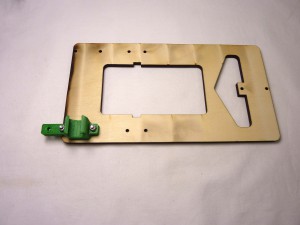 |
Repeat this layout for the other two bearing holders. |
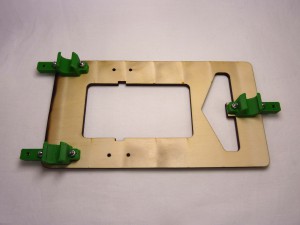 |
Using the M3x20mm cap screws and nylocs attach one of the belt clamps. The clamp should be on the same side of the sled as the bearing holders. Leave the nuts loose for the moment….. |
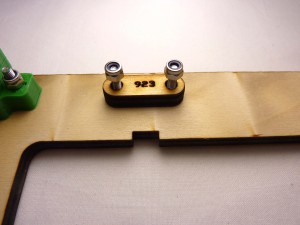 |
…and repeat this for the other belt clamp. |
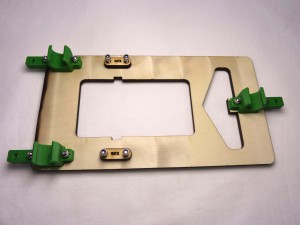 |
Push the linear bearings into the bearing holders from the side. Don’t try to clip them in from the top. They should be an interference fit and should stay where they are put. |
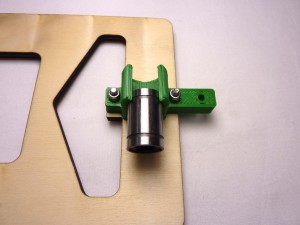 |
When correctly fitted, the linear bearing should protrude by the same amount from each end of the bearing holders. |
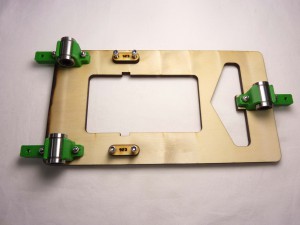 |
Insert a standoff into one of the bearing holders from the other side of the carriage….. |
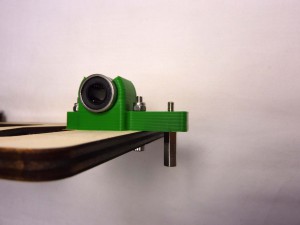 |
….and secure with an M3 nyloc nut |
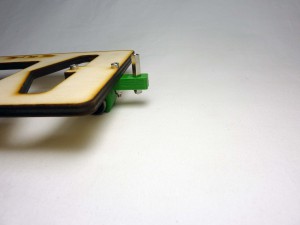 |
Repeat this for the remaining two bearing holders. |
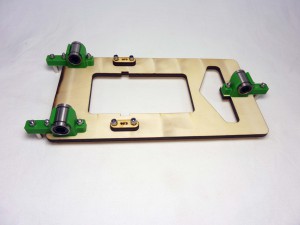 |
Y-rod alignment
Loosen the Y bar clamps. Adjust one of the bars(either one) such that the gap between the M8 nut of the frame vertex, and the nut of the bar clamp is 27mm. There is a gauge to do this on the jig. Tighten the nuts to secure the rod in this position, and repeat for it’s other end. Do not do this for the other rod…. |
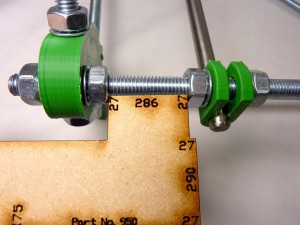 |
Instead use the jig to position the 2nd rod such that the gap between their inside edges is 175mm. Loosely tighten the clamps to secure their position. |
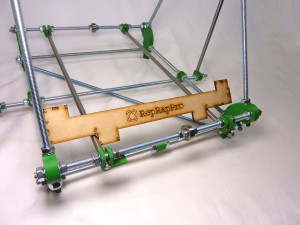 |
Y motor & Idler
# |
Component |
Qty |
Type |
325 |
Y motor bracket |
2 |
Lasercut |
322 |
Belt guide |
4 |
Printed |
279 |
623 bearing |
3 |
Hardware |
946 |
13mm Nylon spacer |
1 |
Hardware |
112 |
M3x25mm cap head screw |
2 |
Fastener |
212 |
M3 washer |
8 |
Fastener |
408 |
NEMA 17 stepper motor |
1 |
Hardware |
389 |
18-tooth MXL pulley and grub screw |
1 |
Hardware |
|
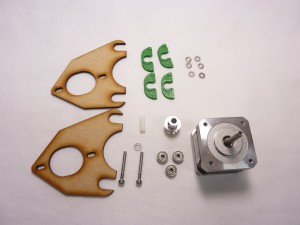 |
The pulley has a threaded hole in it for a grub screw to hold it on the motor shaft. This should be supplied fitted, but if not, screw the grub screw into the pulley a short distance. |
 |
Take an MXL pulley and push it onto the motor shaft, taking care to note its orientation. Install the pulley with the pulley teeth closest to the motor body. The motor shaft has a flat on it; align the grub screw with this, and tighten the grub screw using a 1.5mm Allen key. |
 |
Leave a gap of about a millimetre between the pulley and the motor body, so the pulley can turn freely, and not rub against the motor body. |
 |
Begin by inserting at M3 washer and M3x25 cap screw through both slots of one of the lasercut motor mounts.On the opposite side, on the cap screw closest to the semi-circular cut out insert two washers, then three 623 bearings and another two washers. |
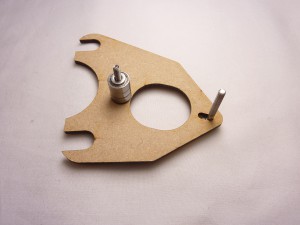 |
On the other cap screw insert 1 x M3 washer, the 3mm nylon spacer and finally another washer…. |
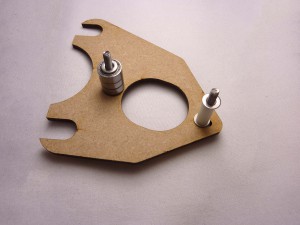 |
then fit the other motor mount onto the cap screws. Again, note the orientation. |
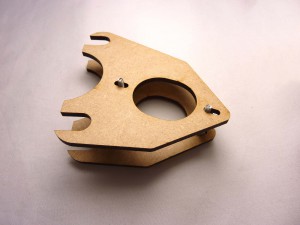 |
Screw this assembly to the motor using the cap screws. The socket for the motor should be on the opposite side when in the orientation shown in the photograph. Check the position of the pulley to ensure the pulley lines up with the centre of the bearings as shown; if needed loosen the pulley and slide along the shaft before re-tightening . |
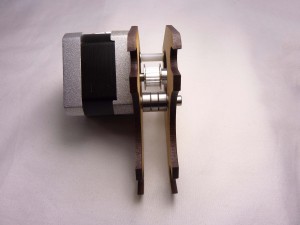 |
On the side of the machine with the Y motor spacer (back), clip two belt guides either side of the bearing. The features of the belt guides should face the bearing |
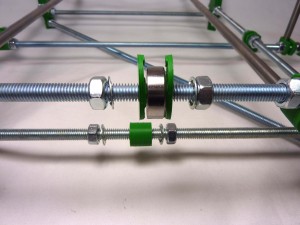 |
Attach the Y motor bracket to the frame, with the laser cut pieces around the outside of the Y motor spacer and belt guides. Loosely secure using the M8 nuts. No need to do this too tightly yet, this isn’t the motors final position. |
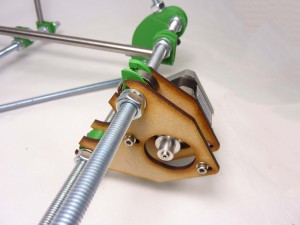 |
On the front side of the machine, clip the other two belt guides either side of the bearing. The features of the belt guides should face the bearing. This is the Y Idler. Secure with the M8 nuts. |
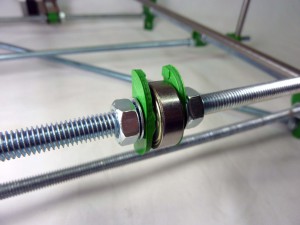 |
Fitting the sled
Slide the 395mm Y rods partly out of the machine, put the sled onto them, and refit their free ends into the frame. The Y-carriage should be orientated so the side with two bearings is on the same side as the y-rod-clamp with the long tab. |
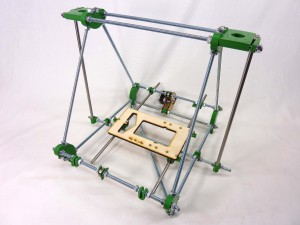 |
Fit the rods back into the bar clamps. Leave all the nuts of Y clamps loose for now. |
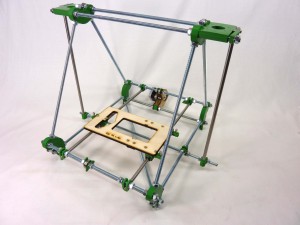 |
Slide the Y sled back…. |
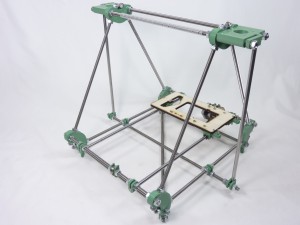 |
and forth. It should run completely freely. If it doesn’t, that means that the rods are not quite parallel – move their ends a little bit using the nuts either side.Gradually tighten the ends of the rods, checking for free running right from end to end all the while as you do so. |
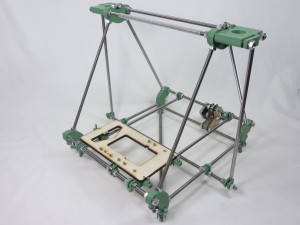 |
Loosen the nuts that secure the Y motor assembly. Move the assembly along the threaded rod to align the Y bearing with the cut out of the Y sled. Then re-tighten the nuts to secure….. |
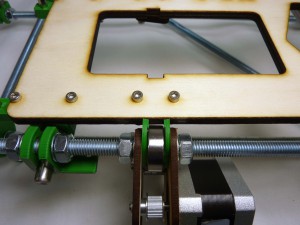 |
…repeat this for the Y idler. |
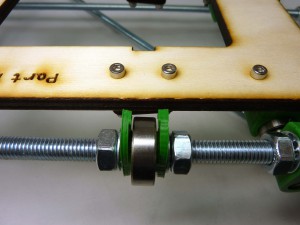 |
Y axis belt
# |
Component |
Type |
337 |
MXL belt |
Hardware |
|
|
NOTE: The MXL belt is usually supplied as one piece, to be shared with the X, Y axes and the X carriage. When you cut off the excess belt you’ll want to retain as much as possible of the remainder. So don’t cut this too long!
Start by loosening the M3 cap screws securing the motor. The slide the motor so that it sits as close to the frame as possible and the cap screws hit the end of the slots they sit in, then retighten the screws. These slots let the motor slide back and forth, and will be used for belt tensioning later. There is an error on this photo. A washer should be between the spacer and the rear lasercut piece. |
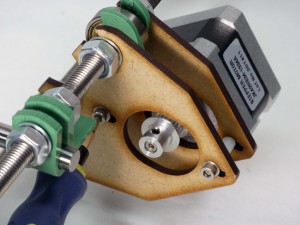 |
It’s easiest to turn the printer upside-down to fit the belt. Start by loosening the belt clamp closest to the Y motor slightly, and insert the belt before re-tightening. The teeth should face the Y sled and the belt should be aligned with the slot of the Y sled as shown. The belt should be facing inwards towards the Y sled. |
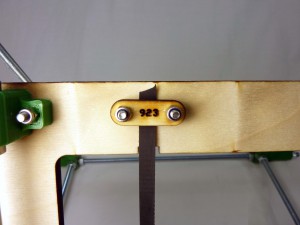 |
Run the belt through the hole in the Y sled, back outwards the Y motor around the 608 bearing, the pulley and over the top of the 623 bearings in the Y motor assembly. |
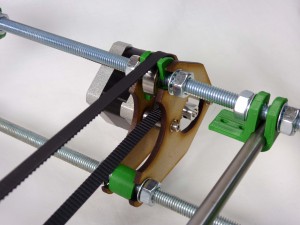 |
Then along to the idler end, around the 608 bearing and back to the belt clamp |
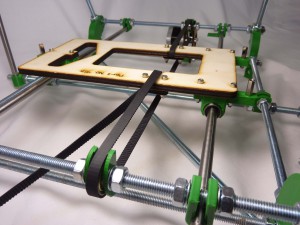 |
Loosen the other belt clamp and secure the belt using the cap screws.The belt doesn’t have to be particularly tight – you will adjust the tension with the Y motor, in a minute. Check the belt lines up by eye. The top should be in line with the bottom and the belt should be square where it sits under the clamps. |
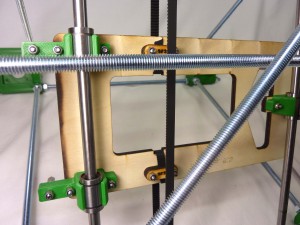 |
Tighten the y axis belt by loosening the two M3 cap head scews securing the y motor. Pull the motor back in the slots, then re-tighten the screws. If you run out of adjustment, you need to tighten the belt using the belt clamps. If you pluck the belt between the 608 bearings (the longest part of the belt), you should hear a low note. The belt doesn’t need to be too tight – check that you can still easily move the Y carriage back and forth. |
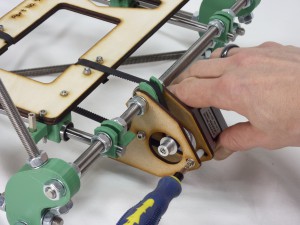 |
This shows the belt fully fitted. Move the y-carriage back and forth, making sure everything on the Y axis stays in line and runs freely, from one end to the other and back. |
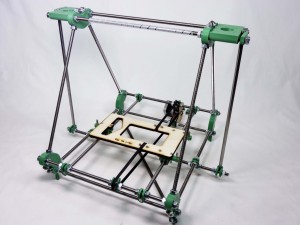 |
Y axis finished
The finished assembly. |
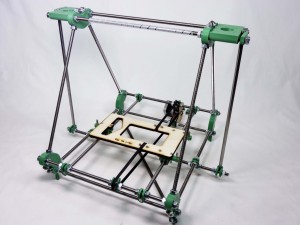 |