Build Instructions – Base Assembly – Tower Assembly – Panels and Rods – Effector Assembly – Extruder Drive
Hot End Assembly – Electronics – Bed, Top Plate and Belts – Commissioning – Printing – Troubleshooting
This page describes the Duet 2 Maestro electronics shipped with Fisher kits from August 2019. If you have an earlier Fisher it will have a Duet 0.6, which is described here.
Goal
By the end of this section, you will have wired up the electronics and installed it in the printer frame (view from underneath).
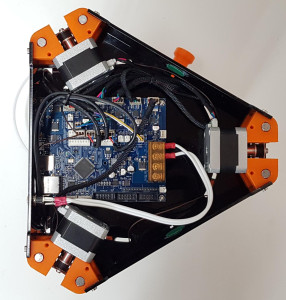
Side Panel Wiring
You will need the following parts:
# |
Component |
Qty |
Type |
|
1303.2 |
Side Panel |
1 |
Laser cut |
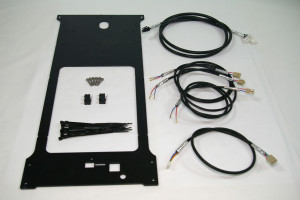 |
242 |
M3x16mm cap head screw |
4 |
Fastener |
185 |
Microswitch |
2 |
Electronics |
133 |
Cable ties 2mm |
as needed |
Electronics |
6201 |
Hot end loom – 700mm |
1 |
Wiring |
1198 |
End stop loom – 500mm |
1 |
Wiring |
552.1 |
End stop loom – 600mm |
1 |
Wiring |
1199 |
End stop loom – 800mm |
1 |
Wiring |
789 |
Motor wiring loom – 500mm |
1 |
Wiring |
|
Extruder drive (not shown) |
1 |
Assembly |
257 |
M3 x 12mm cap head screw |
2 |
Fasteners |
Remove the protective film from the acrylic panel. |
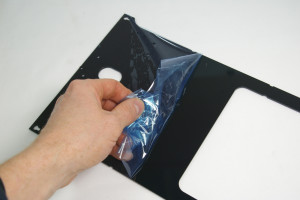 |
The microswitches fit to the inside of the panel. Note the orientation of the bottom of the panel; this fits around the Duet electronics. |
 |
Fit the microswitches with cable ties, as you did with the first microswitch. Make sure the cable tie end is towards the top of the panel. |
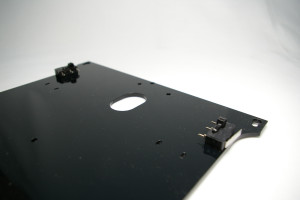 |
The endstop looms have two wires, and there are three different lengths of looms. |
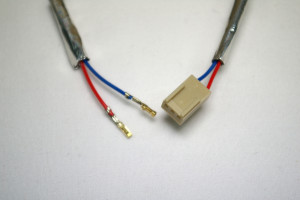 |
The hot end loom has eight wires. Note that if you are upgrading from a Duet 0.6 to a Duet Maestro this cable has changed. You won’t be able to use your Duet 0.6 cable on a Duet Maestro. |
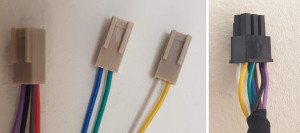 |
An extruder motor wire has four wires. This is the longest motor wire (500mm). The fourth wire is sometimes yellow, sometimes black. This has no significance. |
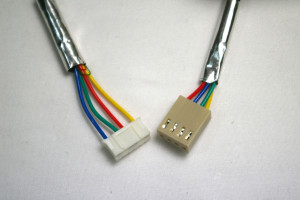 |
Mount the shortest endstop loom (500mm), the hot end loom and the extruder motor loom on the left side. The other two endstop looms go on the right. |
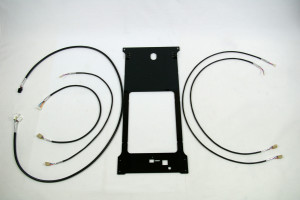 |
Left side: Attach the endstop loom to the microswitch on the left hand side. Put the crimps on the outside tabs of the microswitch, NOT the middle one. Polarity is not important. Try not to bend the crimps on the microswitch tabs, or they will become loose. |
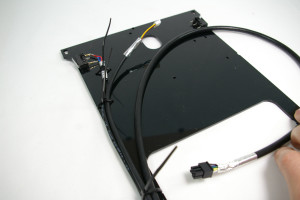 |
Fasten the endstop loom in the top cable tie, the endstop and the extruder loom in the next one down, and all three looms in the rest of the cable ties. Don’t fully tighten the cable ties yet, so you can adjust the wire position. |
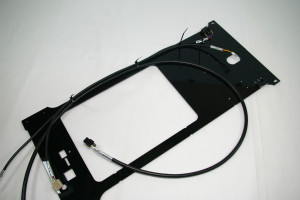 |
Right side: connect the shorter endstop loom (600mm) to the microswitch. |
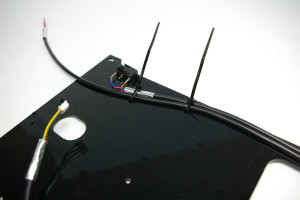 |
Cable tie both wires in all of the positions. Do not pull the ties tight yet. |
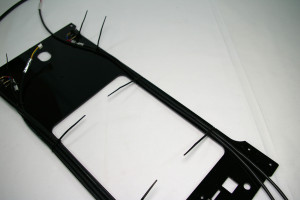 |
Attach the extuder drive to the panel, using two M3x12mm cap head screws from the outside. Connect the extruder motor loom to the extruder motor. |
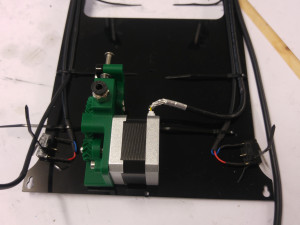 |
Fit the Panel and Connect
As with the other panels, lift the printer up off the surface, and fit the top of the panel onto the screws in the idler printed part. |
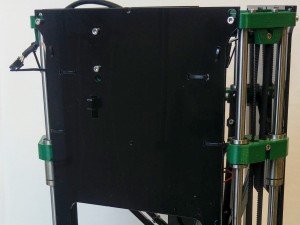 |
Line up the bottom with the holes in the motor mounts, and fasten with four M3x16mm cap head screws. Make sure the wiring looms fit into the slots in the base plate. |
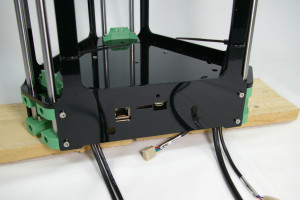 |
Connect the Bowden tube to the extruder. Push the bowden tube into the pneumatic fitting. |
 |
Position the nozzle of the hot end touching the approximate centre of the bed by hand. This is a top view showing what the Bowden tube length should be like – you want a loop so the hot end is free to move everywhere over the bed without causing a tight bend at either end, but you don’t want it so long that it flaps about.
If you need to, shorten the tube with a sharp blade. Take care to make a right-angled cut. |
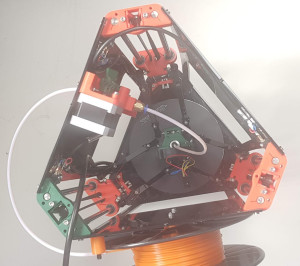 |
Connect the third microswitch in the same way as the other two, and cable tie it to the panel. |
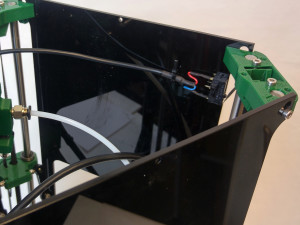 |
Connect the hot end loom to the hot end. It is useful to cable tie the loom loosely to the Bowden tube, above and below the connector. Check that plugging the connectors together has not pushed any of the crimps partly out of their shells. If it has, use a narrow-bladed screwdriver to push them back. |
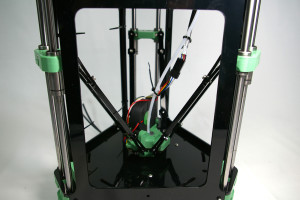 |
Now adjust the cable lengths until everything is neat, moving the mechanism between the top and bottom and side to side to check. The hot end loom and Bowden tube should move together. Try and get a nice loop, so they move cleanly as the effector moves up. |
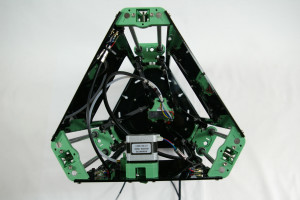 |
Tighten and trim all of the cable ties. Move the carriages up and down their full range of movement, making sure they don’t catch on anything. Check that the heads of the cable ties don’t get in the way, and that the wiring looms are neat against the side panels. Adjust any cables as needed, and make sure the hot end loom and Bowden tube don’t catch on anything. |
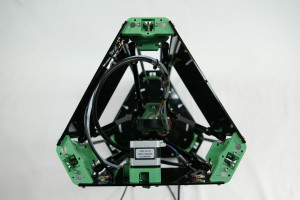 |
Bed Probe Wiring
You will need the following parts:
# |
Component |
Qty |
Type |
|
1203.1 |
Bed probe loom – red or brown (old image; the latest wires are equal length) |
1 |
Wiring |
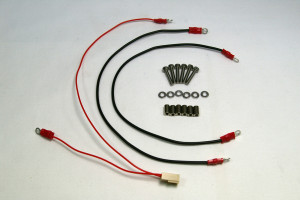 |
1202 |
Bed probe wire – red or brown |
2 |
Wiring |
257 |
M3x12mm cap head screw |
6 |
Fastener |
212 |
M3 washer |
6 |
Fastener |
1253 |
M3x8mm spacer |
6 |
Hardware |
Fit the Power Jack
You will need the following parts:
# |
Component |
Qty |
Type |
|
193 |
Power jack |
1 |
Electronics |
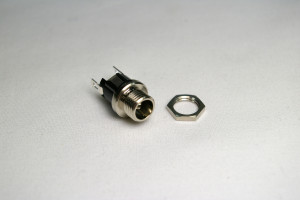 |
455 |
Power jack nut |
1 |
Electronics |
Turn the printer over. It can rest on its top as you connect the wiring. The DC power jack may now be fitted as shown, next to the Ethernet socket. In this orientation the central pin of the three should be on top. |
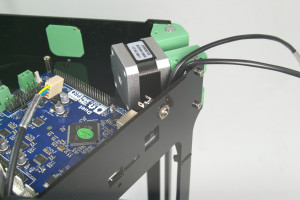 |
Duet 2 Maestro Connections
Wiring Diagram
The instructions below show the fitting of the wiring. If in doubt, refer to this wiring diagram.
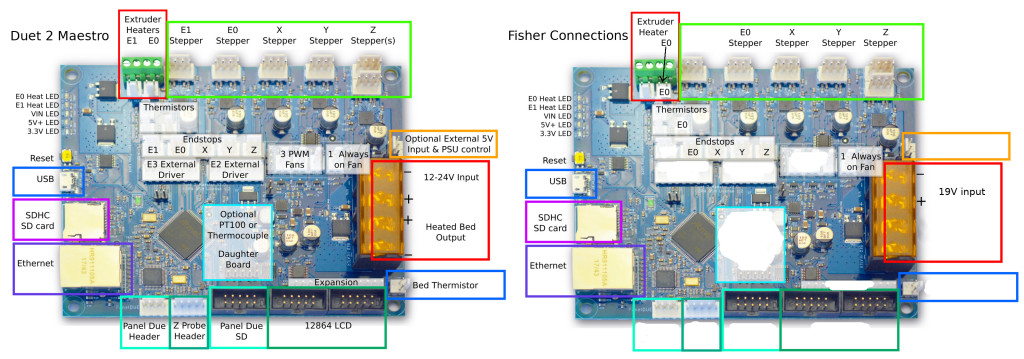
On the left are all the Duet 2 Maestro’s available connections. On the right is the same picture, but with the only the connections used in Fisher shown.
Duet Wiring Connections
In this section you will connect the wiring looms to the Duet, as shown in the pictures below. You can also refer to the wiring diagram above. You will need the following parts in addition to the looms you have already fitted to the machine:
# |
Component |
Qty |
Type |
|
6202 |
DC cable – 250mm |
1 |
Wiring |
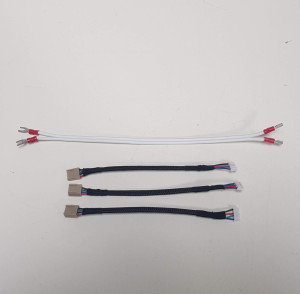
|
477 |
Motor looms – 160mm
|
3 |
Wiring |
Here is the Duet fitted, but with no looms attached.
The end of the looms to be attached are marked in red.
First check that the five jumpers on the board with the red dots in the picture are connected as shown, and that there are no other jumpers elsewhere.
Remember that you can click on a picture to get a large version. |
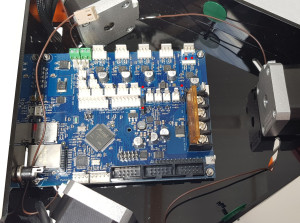
|
Start with the extruder drive motor loom. This is the longest motor drive cable, and it runs up the inside of the machine on the side panels to the extruder drive. The red wire should go on the left, as in the picture. |
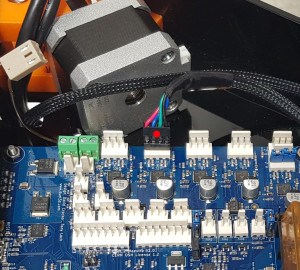 |
Next use the three short 4-way motor looms to attach the motors to their driver connectors on the Maestro. The motors and the ends of their looms are all labelled X, Y, and Z here. |
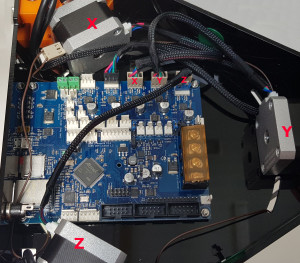 |
Next connect the three two-way sockets on the end of the hot end loom. Going from the back to the front and left to right in this picture, the connections are the heater (four wires in two sockets: red/brown and purple/black); the thermistor (blue and green); and the fan (white and yellow).
Make sure the fan goes in the always-on Maestro connector. It must run all the time the machine is switched on. |
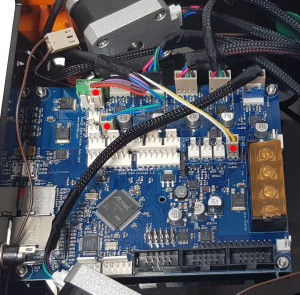
|
Next connect the bed-stop loom that runs to the three sphere/cylinder contact breakers at the three corners of the bed. This is a three-way connector with only two wires in. (The third central unused connection is to power endstop detectors that need a supply. In the Fisher all the endstops are simple switches.) |
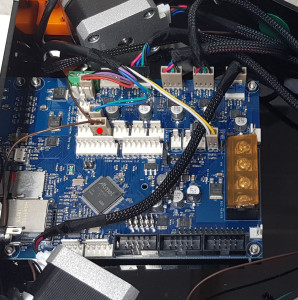 |
Next connect the three column endstop switch connectors. The columns X, Y, and Z are labelled in the motor loom connection picture above. Trace the microswitch at the top of each column corresponding to each motor down along its loom to find which of the three ends is X, Y, or Z. |
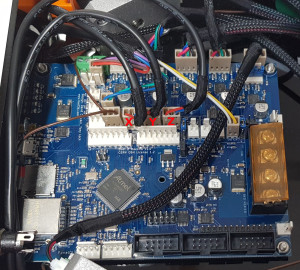 |
Finally connect the power cable. This picture shows the back of the jack socket… |
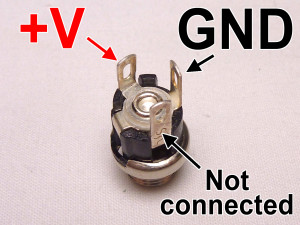 |
…and here is the power cable fitted. The wire with the stripe is Ground (GND), negative. The plain wire is +V, +19V. The transparent cover over the screw connectors flips up on a hinge to the left in this picture so you can get at the screws. Make sure all the connections are solid and tight, but don’t over-tighten the screws or you may damage the Maestro’s printed circuit board. |
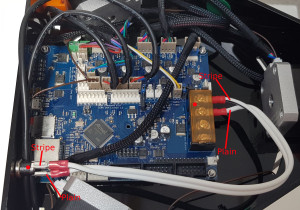 |
All the wiring connections fitted. |
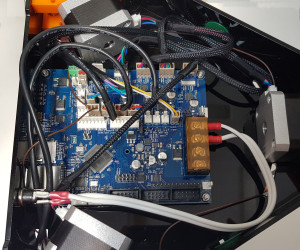 |
With all the wiring fitted, tidy up the wiring so that it all fits below the level of the acrylic side panels. You can use a couple of cable ties to help. |
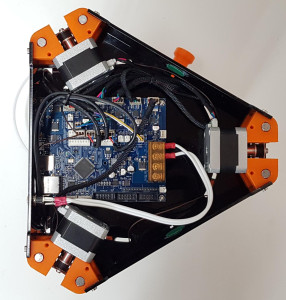 |
Back – Hot End Assembly Next – Bed, Top Plate and Belts